Did you know that construction costs in the United States surpassed $1.3 trillion in 2020? That’s a staggering figure that highlights the massive scale of the construction industry and the significant expenses involved in every project.
Construction companies face numerous challenges when it comes to maximizing profits. Despite their expertise in building projects, factors such as low-bidding practices, labor shortages, rising costs of building materials, and intense competition can diminish their bottom line. To ensure profitability, construction companies need to focus on various strategies, including productivity improvement, cost management, accurate estimation, profitability goal-setting, and effective project management.
Key Takeaways
- Construction costs in the U.S. exceeded $1.3 trillion in 2020.
- Maximizing profits in the construction industry requires overcoming challenges like low-bidding practices, labor shortages, rising costs, and competition.
- Improving productivity is crucial for controlling costs and avoiding delays in construction projects.
- Understanding and managing costs, both direct and indirect, is essential for profitability.
- Setting profitability goals and analyzing project results can guide a construction company’s growth and success.
Improving Productivity in Construction Projects
Improving productivity is essential for maximizing efficiency and controlling costs in construction projects. By implementing strategies to optimize productivity, construction companies can stay on schedule and meet project deadlines while minimizing delays and expenses.
One of the key factors in improving productivity is careful planning and scheduling. This involves creating a detailed project timeline and coordinating the different tasks and activities involved. By having a clear roadmap, construction teams can ensure that work progresses smoothly and efficiently.
Proper training and equipping workers with the necessary tools and resources are also crucial for maximizing productivity. Well-trained workers are able to perform their tasks more skillfully and efficiently, leading to faster project completion. Additionally, providing workers with modern tools and equipment can help streamline workflows and eliminate unnecessary delays.
Supply chain management plays a significant role in construction productivity. By ensuring a steady and timely supply of materials and resources, construction companies can avoid delays and keep projects on track. Effective supply chain management involves building good relationships with suppliers, optimizing inventory management, and implementing efficient procurement processes.
Improving productivity in construction is not just about working faster; it’s about working smarter. By identifying and addressing factors that negatively impact productivity, such as poor scheduling, accidents, and rework, construction companies can create a more efficient and productive work environment.”
Accidents and rework can have a significant negative impact on productivity. By prioritizing a strong safety culture on construction sites and implementing robust quality control measures, companies can reduce the risk of accidents and minimize the need for rework, thus improving productivity.
Regular monitoring, analysis, and adjustment of productivity factors are essential for continuous improvement. Construction companies should evaluate their productivity metrics, identify areas for improvement, and implement corrective measures accordingly. This includes analyzing project data, tracking performance indicators, and addressing any bottlenecks or inefficiencies that may arise.
Improving productivity in construction requires a holistic approach that encompasses planning, training, resource management, and continuous improvement. By prioritizing productivity, construction companies can increase efficiency, reduce costs, and ultimately enhance their bottom line.
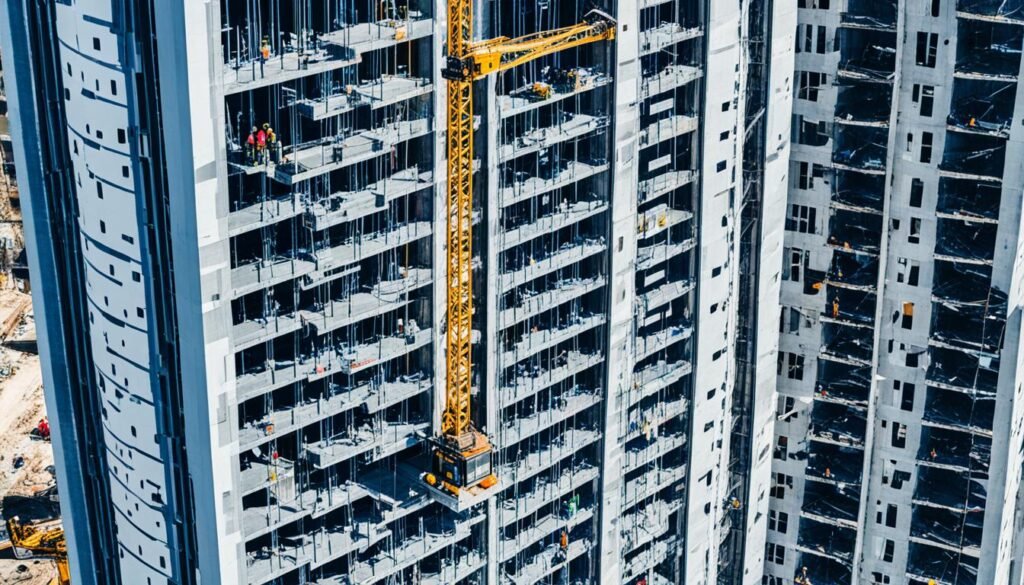
Understanding and Managing Costs in Construction
Managing costs effectively is crucial for construction companies to maintain profitability and achieve financial success. By implementing construction cost analysis techniques and estimating job costs accurately, companies can optimize their operations and make informed decisions that positively impact their bottom line.
Construction cost analysis involves tracking job costs throughout the project lifecycle. This includes both direct costs, such as labor, materials, and permits, as well as indirect costs like overhead expenses. By keeping a close eye on expenses, companies can identify areas where costs can be minimized and find opportunities to increase efficiency.
Accurately estimating job costs is a fundamental aspect of managing construction costs. By conducting thorough assessments of project requirements, including labor, materials, subcontractors, and equipment, construction companies can create comprehensive cost estimates. This enables them to submit more competitive bids and avoid costly surprises during the project execution.
Moreover, construction companies should also prioritize effective management of indirect costs, such as insurance, taxes, utilities, and office supplies. These expenses, although not directly tied to specific projects, can significantly impact the overall profitability. By analyzing and controlling these overhead expenses, construction companies can improve their financial performance and maintain a healthy profit margin.
Importance of Construction Cost Analysis
Construction cost analysis provides crucial insights into the financial health of a construction company. It enables companies to identify cost overruns, inefficiencies, and areas for improvement. By examining historical data and comparing it to the planned budget, construction companies can implement corrective actions, develop more accurate cost estimates for future projects, and enhance their overall financial performance.
Optimizing Construction Cost Management
To effectively manage costs in construction, companies should consider implementing the following strategies:
- Regularly track and review job costs to identify areas of improvement
- Use construction management software to streamline cost analysis processes
- Utilize historical data and industry benchmarks to create accurate cost estimates
- Collaborate closely with suppliers and subcontractors to negotiate better pricing
- Optimize resource allocation to minimize waste and maximize efficiency
By adopting these strategies, construction companies can enhance their ability to manage and control costs effectively, leading to improved profitability and long-term success.
“Understanding and managing costs is essential in the construction industry. By tracking job costs, estimating accurately, and conducting construction cost analysis, companies can optimize their financial performance and achieve profitable growth.”

Setting Profitability Goals and Analyzing Results
Setting profitability goals is a crucial step to improve your construction company’s financial performance. By defining specific goals, you can guide the direction and growth of your business. Start by assessing your current profit margin and determine the desired increase you aim to achieve.
Once you have set your profit margin goals, track your progress regularly. Monitor your project results to evaluate the estimated versus actual costs. This analysis helps you identify areas of improvement and make necessary adjustments for future bids and projects.
When analyzing the project results, pay attention to various cost factors such as labor, materials, permits, and overhead expenses. Comparing these costs to your estimates allows you to spot discrepancies and understand where your profitability can be enhanced. It also helps you identify trends and patterns that can be useful for future budgeting and planning.
By setting profitability goals and analyzing project results, you can gain valuable insights into your construction company’s financial performance. This proactive approach empowers you to make informed decisions, optimize your operations, and work towards achieving higher profit margins in the construction industry.
FAQ
What is the biggest expense in construction?
The biggest expense in construction projects is typically labor costs. Skilled workers, such as carpenters, electricians, and plumbers, command high wages, and large construction projects require a significant workforce, resulting in substantial labor expenses.
What are the major expenses in construction?
In addition to labor costs, other major expenses in construction include materials, equipment, permits, insurance, and subcontractor fees. These costs can vary depending on the type and scale of the project.
How can construction companies better manage their expenses?
Construction companies can better manage their expenses by carefully estimating costs, tracking job costs, prioritizing productivity and efficiency, negotiating favorable prices with suppliers, and implementing effective project management practices.
How can construction companies improve their profit margins?
To improve profit margins, construction companies can focus on improving productivity, understanding costs, estimating for profit, setting profitability goals, and effective project management. By optimizing these areas, companies can increase efficiency, reduce costs, and enhance profitability.